Gravelotte Project, South Africa
Overview
Magnum’s 74%-owned Gravelotte Project is located in the Limpopo Province of South Africa.
Emeralds were discovered in the province in 1927 and since then, several companies have explored for and mined within the broader region for emeralds.
From 1929 to 1982 the total recorded emerald production from the Gravelotte Project, as well as the area surrounding the nearby Gravelotte township, was nearly 113 million carats.
It is reported that during the 1960’s the Gravelotte Project itself was the largest emerald mine of its type in the world, employing over 400 sorters.
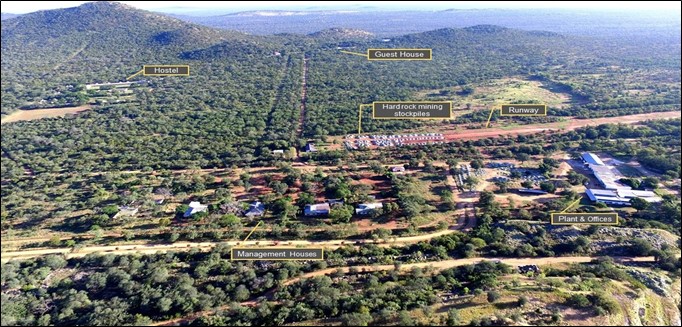
Figure 1: Gravelotte Infrastructure
Why is Magnum at Gravelotte?
The Gravelotte Project provides Magnum with a medium term production opportunity in the niche commodity of emeralds where demand is growing.
The project offers established infrastructure, existing and accessible open cuts together with extensive low grade dumps, a large (albeit incomplete) historic data base, a nearby and available work force, local on-site technical expertise and a nearby township that can serve as a supply centre.
The Company has maintained and refurbished much of the extensive mine site infrastructure at Gravelotte including offices, laboratory, workshops, garages, management accommodation complex and a mine hostel to accommodate mine workers.
The mine site is well situated with utilities and logistics being serviced by ESKOM grid power, has a sealed road to the mine gate and has a working airstrip.
The Next Steps to Development
The Gravelotte Project is now at the pre-development stage and activities focused on finalising mine planning and preferred sorting options.
In addition, final quotations for the processing equipment (expanded crusher and washing and screening circuit) were sourced.
Mining operation will commence within the Cobra North pit where current planning is for around five years of production before potential underground mining is required.
The Cobra South and Discovery pits will provide additional sources of material for potential expansion of operations.
Geology
The emerald mineralisation at Gravelotte is contained within a mafic schist that is bounded by a granite and a felsic porphyry. Historic production and drilling data shows that whilst the large majority of the schist is emerald mineralised, the grade distribution is inhomogeneous.
As a consequence the majority of grade control within the proposed mining operation will rely on other indicators of emerald mineralisation such as the presence of discolouration of the schist, biotite alteration and development of pyrite.
This grade control will be carried out through the logging of the blast hole material and visual examination of the run of mine material.
Sorting Options for the Recovery of Emeralds
The Company has been in continuous engagement with leading manufacturers of material sorting solutions. Sorting of emeralds is the tertiary stage in the processing and the Company is assessing the two main options available – Optical sorting or sorting using XRF technology.
The use of either of these technologies effectively mechanises the operation and removes the requirement to hand sort.
Whilst the use of XRF technology during the trial mining programme was technically successful, it did suffer from some instrument related outages which did affect the processing rate. As a consequence and also because of recent advances in colour sorting technology for emeralds, it was decided that the Optical technology should also be assessed.
Optical sorting trials carried out on samples of Gravelotte ore shipped to Germany showed very positive results across all three measures – accuracy, precision and throughput.
The finalisation of this test work and the final XRF testing will allow the Company to confirm both costs and lead time for the delivery of appropriate sorting technology.
Impact of Covid-19
The Covid-19 virus had a significant impact of the operations at Gravelotte during 2020. The Company managed to maintain staff and security on site but the movement of the various technical consultants was severely restricted.
As a consequence the large majority of the technical and financial analysis completed, included the trial optical sorting, were completed off-site.